
Lorch was one of only a few manufacturers to ignored the long-time convention that turning a handle to the right would produced an inward movement of the cutting tool and, as a consequence, all versions of this lathe had right-hand thread or "cack-handed" screws as they were commonly known. In bare form the shorter of the two lathes in plain turning form weighed 41 lbs Because it was possible to swap and adapt parts from a number of other Lorch models, the factory also offered a number of special versions including the rare LLPN, a type fitted with a headstock designed for thread chasing where the spindle slide in and out of its bearings under the influence of a master thread and follower.įurther information about this process, together with details of other Lorch lathes on which it was fitted, can be found here. The longitudinal travel of the top slide was 90 mm 3.
#Lorch lathe instruction manual full#
The recommended countershaft speed was rpm with an allowable maximum spindle speed of a little over double that.īeautifully constructed, the compound slide rest had a usual-for-the-type long-travel top slide and, happily, a full length cross slide that offered superior support even wear to its ways. For collet use both types accepted either a simple drawbar or production-type lever-action quick-closer. Super-hard, ground and lapped the headstock spindle ran at first in adjustable steel bearings early s and then, at some point towards the late s, in bronze replacements. Available with both lever and screw-feed barrels, the tailstock accepted the same collets as the headstock, though the latter appears was supplied without a Morse taper, this centre being carried, in the traditional way, as part of a solid collet. As on some other Lorch models, an epicyclic reduction unit was available that replaced the gear normally carried on the end of the leadscrew the effect was to provide an especially fine rate of sliding feed, a handy aid in getting a good finish on a long job. Unfortunately the rack-pinion gear engaged directly with the rack, instead of through reduction gearing, resulting in a very coarse feed along the bed. With the lever set in the "light engagement" position - and the spring pulling on the cam plate - as the knock-off button hit the bed stop the pivoted bar pulled the pawl out of engagement and the spring rotated the cam plate, so disengaging the clasp nuts.Įxperienced users report that, whilst the automatic disengage would work reliably when using power sliding for ordinary turning jobs, for screwcutting it was better to forgo the luxury of the mechanism and leave the spring force disconnected the full-engagement position. The clasp nuts were closed by the usual kind of snail-slotted cam plate with, in this case, the latter having a V-shaped cut-out in its outside face together with a peg, the end of which was connected by a spring to an arm of the end of the shorter lever.Īs the plate was turned to engage the nuts, a pawl, on the end of a pivoted bar connected to the disengagement button, was allowed to drop into the V-slot. Some early versions of the lathe had an ingenious method of providing an automatic knock-off to the carriage sliding feed: fitted to the apron were two handles - the shorter to select either "light" or "full" gripping and the longer to control the bronze clasp nuts.

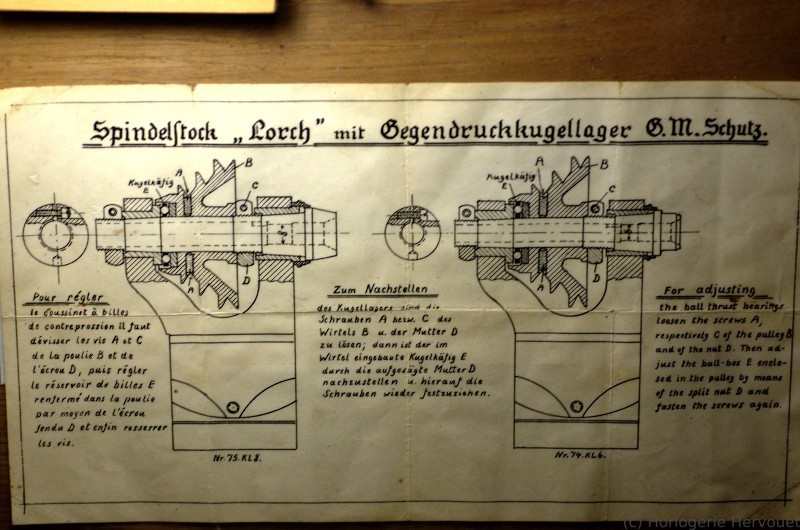
Two bed lengths of and mm Although the carriage was guided by a V-way at the front and a flat at the rear as distinct from the traditional flat-topped, bevelled-edged bed of the plain lathes on this model Lorch used a special form of guide to retain the headstock and tailstock: the arrangement consisted of a front vertical face, together with an angled way at the rear that was cut into the underneath of the slot that ran down the centre of the bed.Īs the locking levers turned, they caused pressure on the angled side to push the units forwards into perfect alignment against the vertical surface. Whilst changewheel guarding on the LN was non existent, the LAN was fitted with a very heavy cast-iron cover that shielded just the front section of the gear train. Clustered together at the right-hand end of the spindle, the backgears were set beneath the spindle line, producing a neat, compact arrangement as also used on the post-WW2 Myford 7 Series. First listed as the Model LA it was to become, when fitted with better guarding of the gears and other small changes, the LAN. Superbly made, to the highest standards, it was the smallest of the company's plain-turning precision toolmakers' models to have a version fitted with backgear and screwcutting by leadscrew and a tumble reverse unit.īy retaining the usual long-travel top slide it was able to maintain the advantages of the ordinary "bench precision" fine turning by hand type whilst being a much more practical and adaptable machine.
